McCloskey TS4065 – 65 FT Tracked Stacker
The McCloskey TS4065 Tracked Stacker is a high-capacity, fully mobile stockpiling solution engineered to streamline material handling in aggregate, mining, and recycling operations. With a conveyor length of 65 feet (18.2m) and a wide 1000mm belt, the TS4065 enables efficient stockpiling directly from crushers and screens — eliminating the need for loaders and reducing double handling.
Applications and Performance
Ideal for:
-
Mobile crushing and screening operations
-
Quarry and aggregate stockpiling
-
Port and bulk material logistics
-
Recycling and demolition sites
The TS4065 enhances site efficiency by reducing reliance on wheel loaders and cutting down on material handling costs. With a quick setup time and intuitive controls, it's ready to boost productivity wherever you deploy it.
Why Choose the McCloskey TS4065?
If you're looking for a mobile stacking conveyor that combines performance, flexibility, and ease of transport, the McCloskey TS4065 is a standout choice. Built for tough conditions and high throughput, it’s the perfect companion for your crushing and screening fleet — helping you move more material, faster, and with fewer resources.
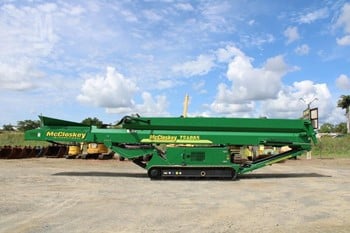
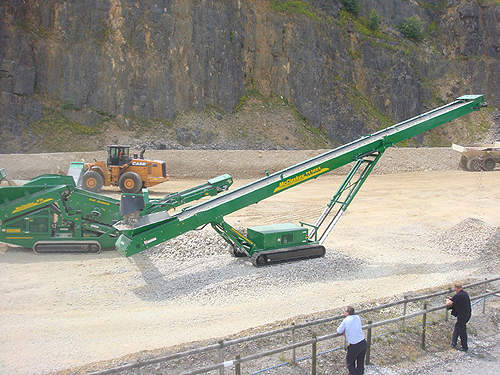
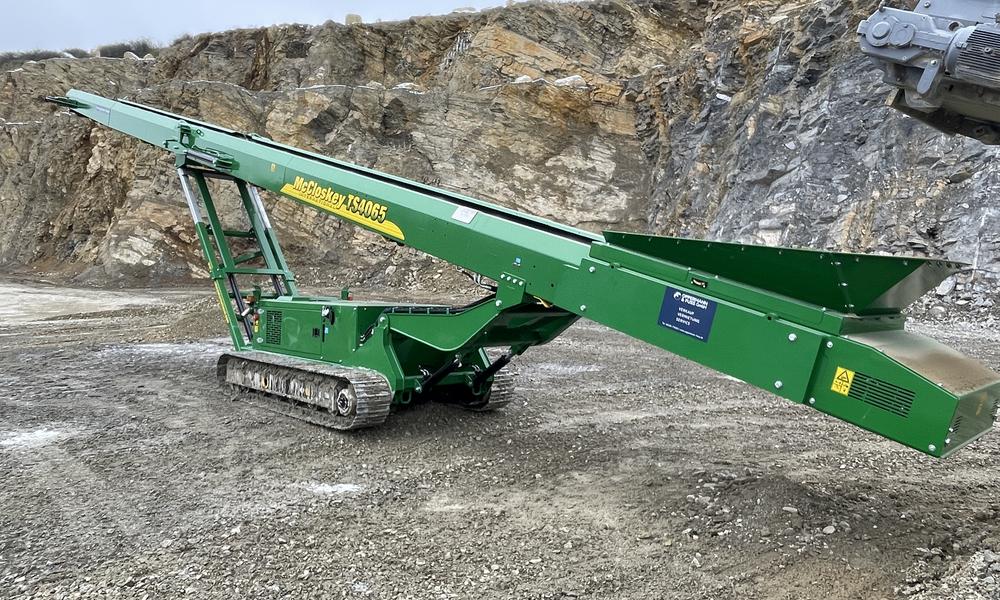
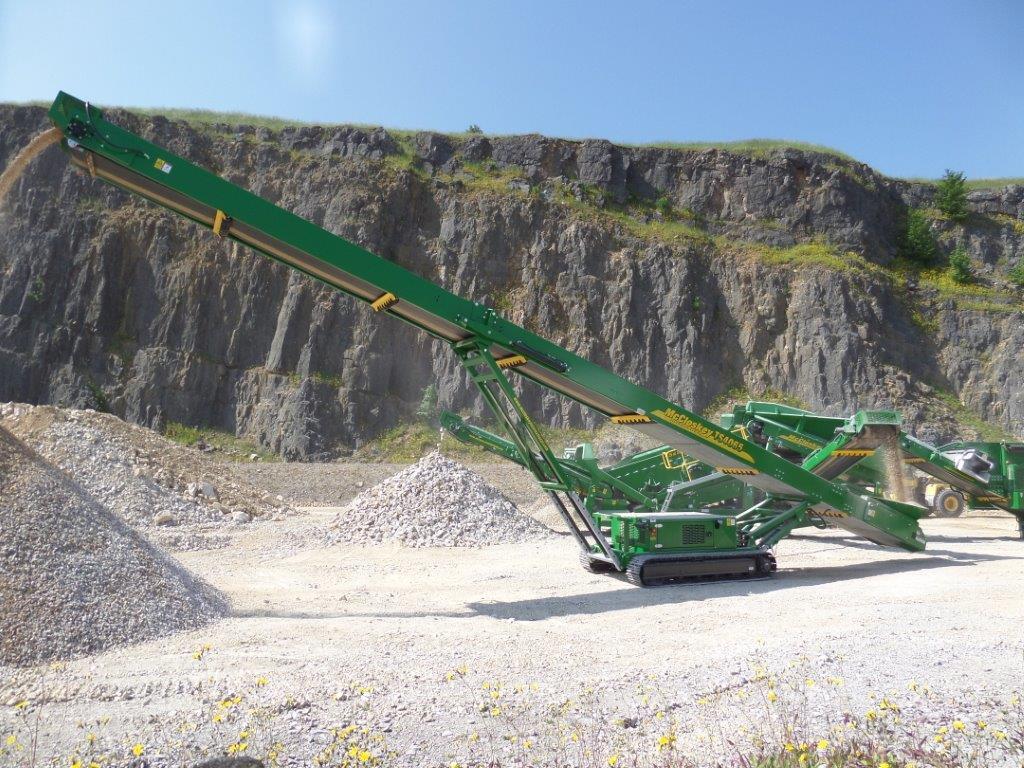
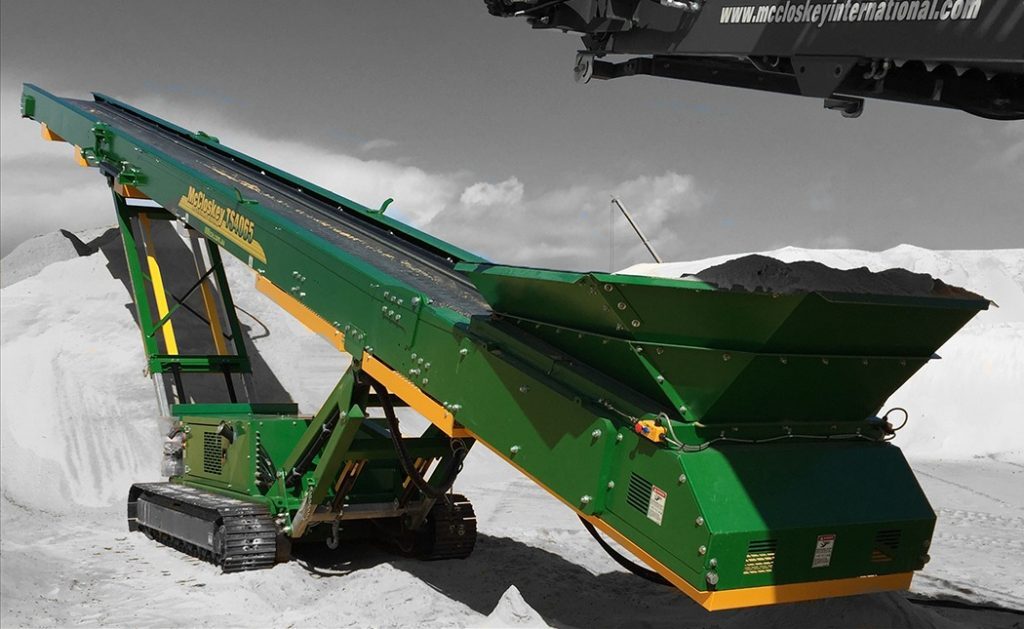
MACHINE BENEFITS
A primary crusher with superior shaping ability, the R5 Impact Crusher fills a variety of roles using just one piece of equipment. The R5’s built in pre-screen’s, post-screens and recirculation conveyor ensures maximum product quality and throughput.
A primary crusher with superior shaping ability, the R5 Impact Crusher fills a variety of roles using just one piece of equipment. The R5’s built in pre-screen’s, post-screens and recirculation conveyor ensures maximum product quality and throughput.
A primary crusher with superior shaping ability, the R5 Impact Crusher fills a variety of roles using just one piece of equipment. The R5’s built in pre-screen’s, post-screens and recirculation conveyor ensures maximum product quality and throughput.
A primary crusher with superior shaping ability, the R5 Impact Crusher fills a variety of roles using just one piece of equipment. The R5’s built in pre-screen’s, post-screens and recirculation conveyor ensures maximum product quality and throughput.