McCloskey J6 Jaw Crusher
Applications and Benefits
The J6 is ideal for:
-
High-capacity aggregate production
-
Primary crushing in hard rock quarries
-
Heavy construction and infrastructure development
-
Processing of oversize demolition material
Why Choose the McCloskey J6?
If your operation requires maximum output, durability, and minimal downtime, the McCloskey J6 delivers. It combines brute power with advanced screening and material handling features — making it the flagship model in McCloskey’s jaw crusher lineup. Designed for serious operators tackling serious workloads.
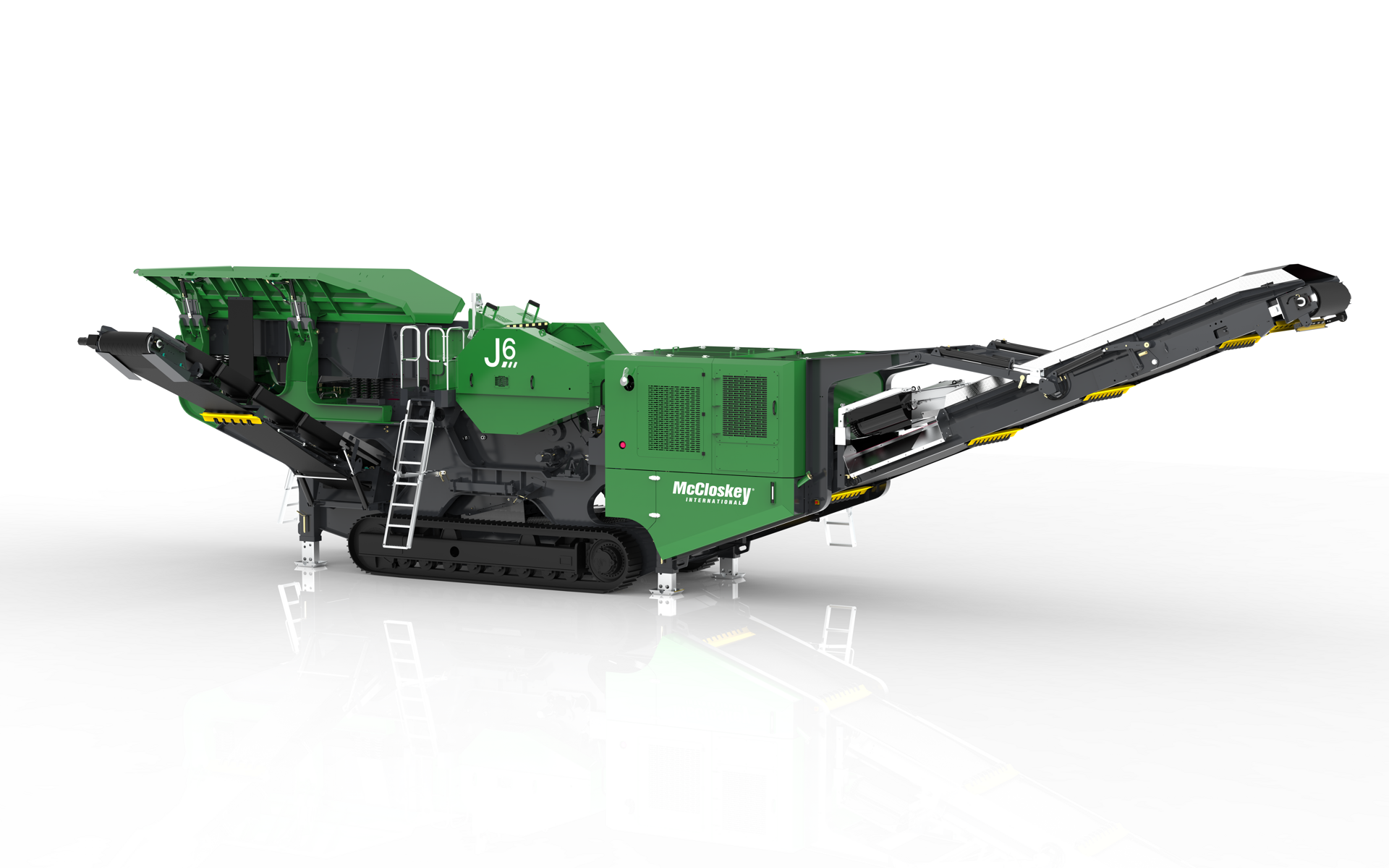
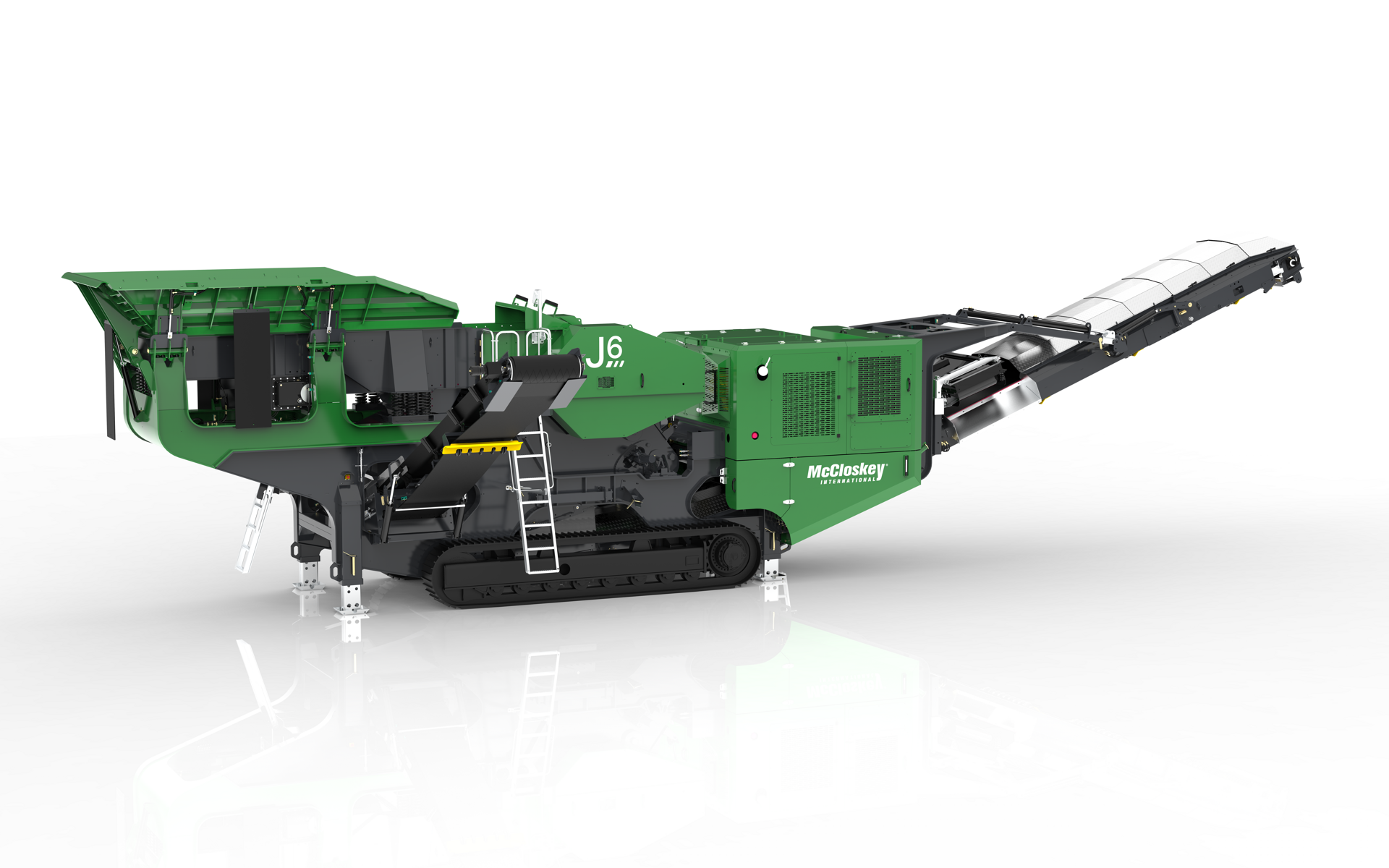
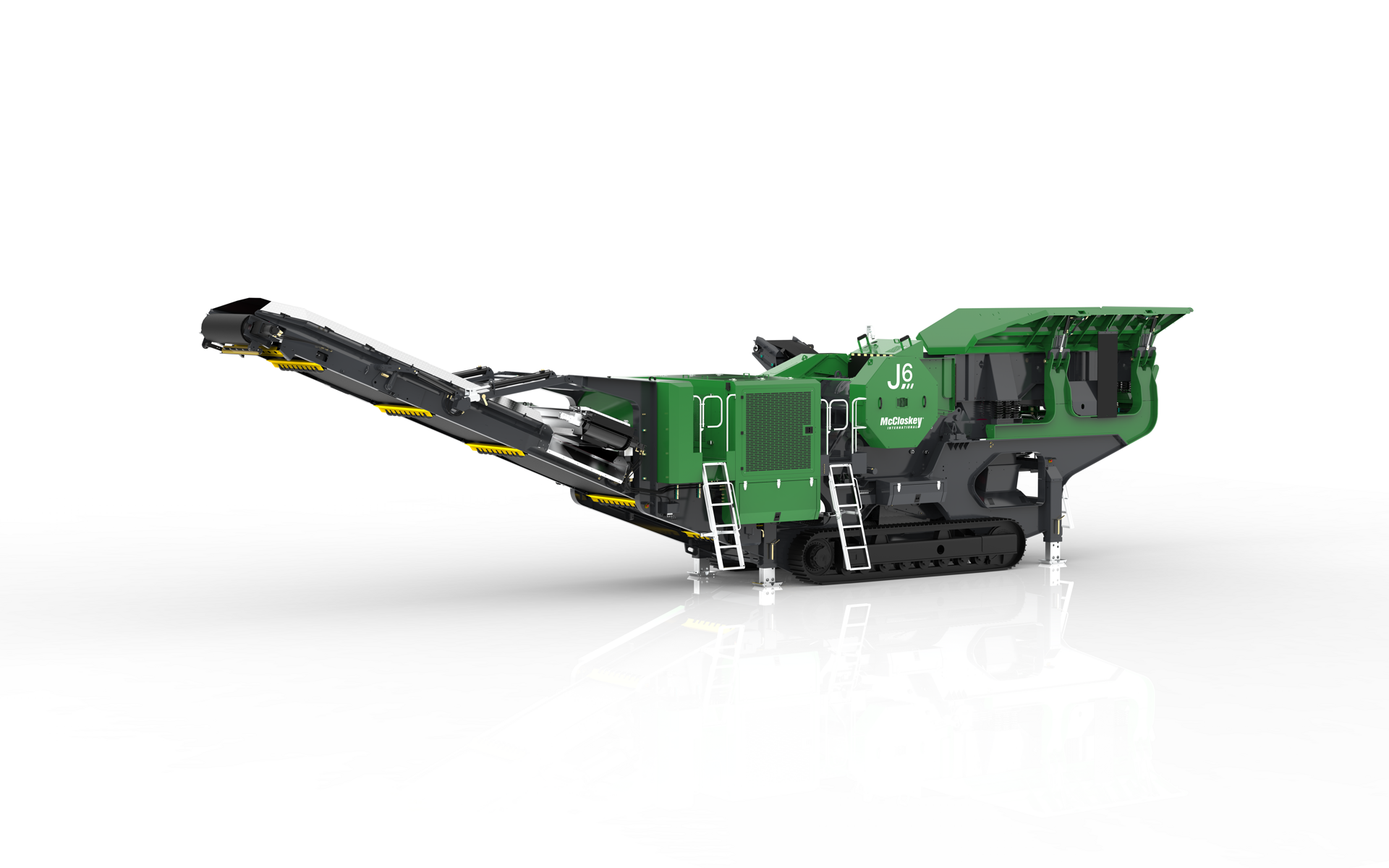
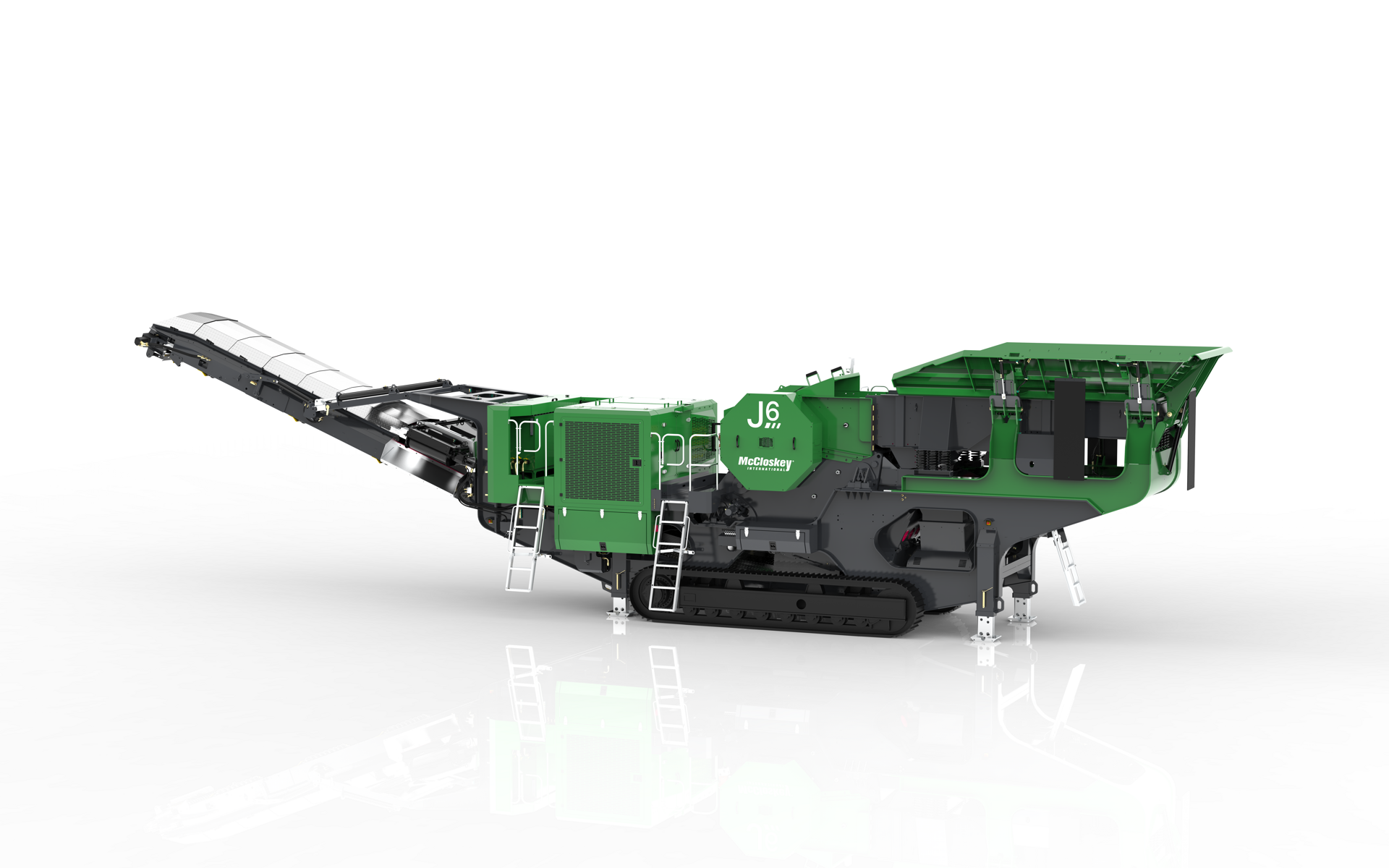
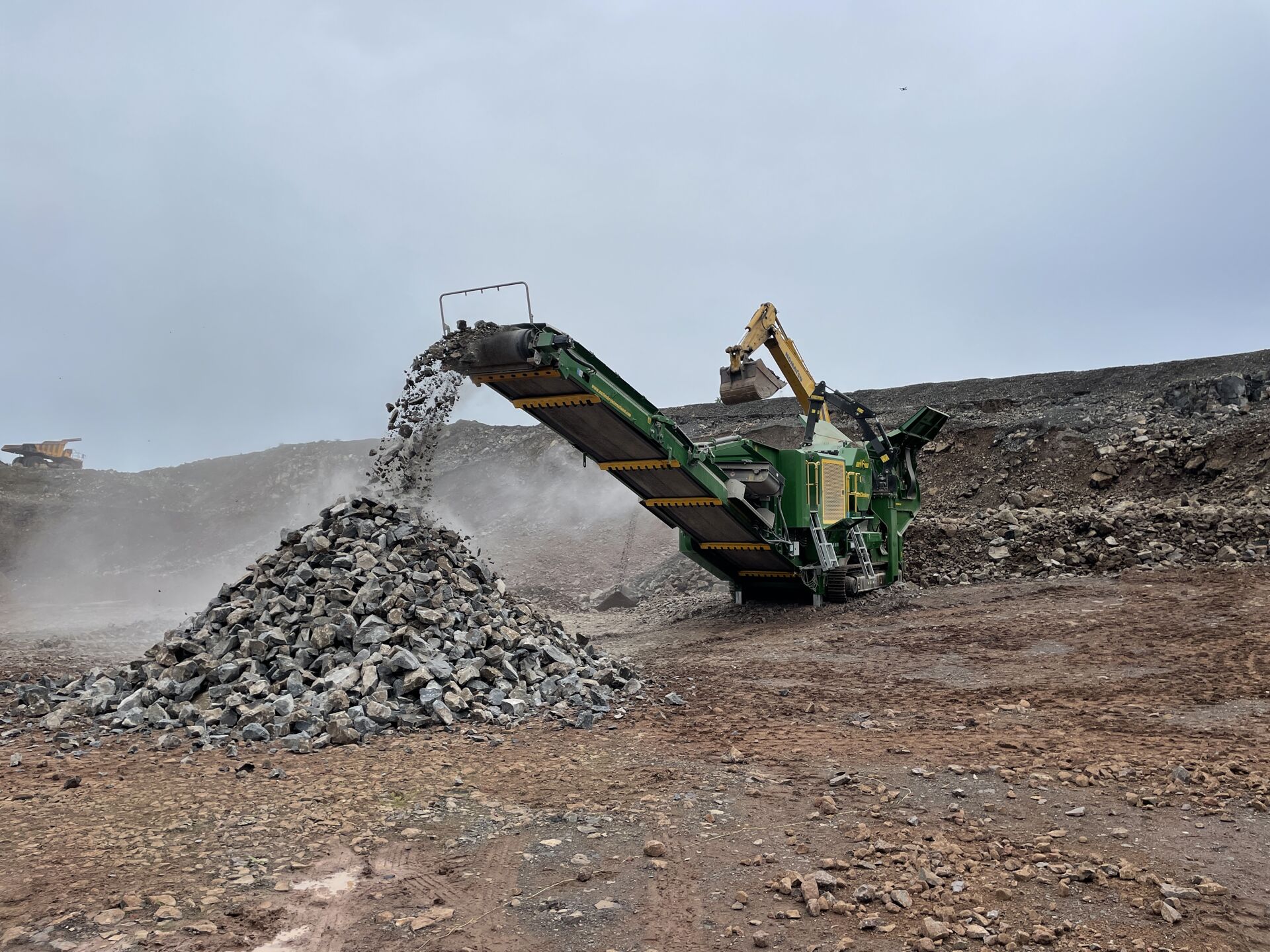
MACHINE BENEFITS
A primary crusher with superior shaping ability, the R5 Impact Crusher fills a variety of roles using just one piece of equipment. The R5’s built in pre-screen’s, post-screens and recirculation conveyor ensures maximum product quality and throughput.
A primary crusher with superior shaping ability, the R5 Impact Crusher fills a variety of roles using just one piece of equipment. The R5’s built in pre-screen’s, post-screens and recirculation conveyor ensures maximum product quality and throughput.
A primary crusher with superior shaping ability, the R5 Impact Crusher fills a variety of roles using just one piece of equipment. The R5’s built in pre-screen’s, post-screens and recirculation conveyor ensures maximum product quality and throughput.
A primary crusher with superior shaping ability, the R5 Impact Crusher fills a variety of roles using just one piece of equipment. The R5’s built in pre-screen’s, post-screens and recirculation conveyor ensures maximum product quality and throughput.